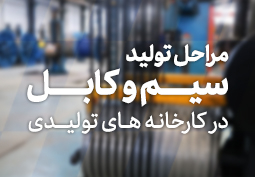
مراحل تولید سیم و کابل در کارخانه های تولیدی
تقریبا میتوان گفت که تولید سیم و کابل در کارخانه های مختلف روند و فرآیند یکسانی دارد اما تولید سیم با تولید کابل تفاوت هایی باهم دارند که در ادامه به ان میپردازیم. در این مقاله سعی بر این داریم تا مراحل تولید سیم و کابل را در یک کارخانه توضیح دهیم پس با ما همراه باشید
محصولات و سبد کالایی شرکت سیم و کابل آمل یک سبد کامل برای استفاده های مختلف است که توانسته هر نیازی را از مشتری رفع کند و با تولید سیم و کابل با کیفیت و تبدیل شدن به یک برند باکیفیت توانسته رضایت مشتریان خود را جلب کند و شرکت سیم و کابل آمل مفتخر است که محصولاتی تولید میکند که با محصولات خارجی در رقابت است و دارای استاندارد های داخلی و خارجی است.
مراحل تولید سیم و کابل
مرحله 1 : نازک کاری
عملیات نازک کاری توسط دستگاه راد انجام میشود که یک دستگاه نازک کن است و همچنین دستگاه فاین که آن هم یک نازک کن است در دو مرحله عملیات نازک کاری انجام میشود. در ابتدای کار مفتول مس 8 میلی متری توسط دستگاه راد به مفتول 1.38 میلی متری تبدیل میشود و این مفتول , ورودی دستگاه فاین است که در دستگاه فاین به درخواست کارخانه و یا سفارش مشتری به مفتول های مناسب تبدیل میشود
دستگاه هایی مثل دستگاه کشش راد وظیفه کشش و نازک کردن مفتول مس را در کارخانه های تولیدی سیم و کابل را دارد که مفتول کامل و اصلی را به صورت خام دریافت کرده و با انجام فرآیند کشش آن ها به مفتول های مورد نظر تبدیل میکند تا وارد مراحل بعدی شود
فرآیند کشش توسط دستگاه راد در داخل روغن انجام میشود که این کار به منظور روانکاری , خنک کاری و شستشو است و در مرحله بعدی مفتول ها بر روی قرقره ها جمع میشوند تا در مرحله استرندر مورد استفاده قرار بگیرند
مرحله 2 : آنیل کاری
تمام مفتول هایی که در مرحله قبل در دستگاه فاین تولید شدند , در محل مشخصی در نزدیکی کوره آنیل کاری جمع آوری میشوند و بعد از اینکه تعداد آنها به حداقل رسیده باشد (تقریبا 54 قرقره) آماده رفتن در کوره و آنیل شدن میشوند و به این شکل مفتول هایی که از مرحله قبل وارد شدند در این مرحله آنیل میشوند و وارد مراحل بعدی میشوند.
مرحله 3 : بانچ کردن یا تاباندن رشته های مس
عملیات تاباندن رشته های مس توسط دستگاه بانچر انجام میشود. موادی که در مرحله قبل آماده شدند یعنی مفتول های آنیل شده که روی قرقره قرار گرفتند جز مواد اولیه این مرحله هستند
برای تولید کابل های چند رشته ای مثل کابل قدرت یا کابل خودنگهدار لازم است دشته های مختلف کابل با ساختار منظمی بهم تابیده شوند که این عملیات توسط دستگاه تابنده انجام میشود. در کابل هایی شبیه به کابل خودنگهدار رشته مغزی که کار اصلی آنها تحمل وزن کابل را میباشد در مغزی کابل قرار گرفته و سایر رشته های کابل با طول تاب معین و جهت چرخش مشخصی به دور آن تابیده میشوند
مرحله 4 : عایق کاری
در مرحله عایق کاری رشته های بانچ شده به عنوان مواد اولیه اصلی و گرانول عایق به عنوان یکی دیگر از مواد اصلی جهت تولید سیم یا زیره کابلی به کار میرود . فرآورده ای که توسط دستگاه اکسترودر تولید شده اگر محصول نهایی سیم باشد جهت بسته بندی به بخش مربوطه ارسال میشود و چنانچه اگر زیره کابلی باشد روی قرقره های مخصوص جمع شده تا رد مدحله تاب زیره یا استرندر به کار رود.
عملیات عایق کاری در دستگاهی به نام اکسترودر انجام میگیرد. اکسترودرها جهت تزریق مواد PVC , XLPE و نیمه هادی به صورت کاملا یکپارچه به عنوان لایه های میانی , عایق یا روکش استفاده میشوند. مواد به صورت تدریجی در داخل ماردون پس از عبور از المنت های حرارتی به تدریج ذوب شده و به صورت خمیری از کلگی دستگاه خارج شده و در خروجی دستگاه اکسترودر قالب هایی تعبیه شده است که این قالب ها متناسب با سایز کابل بوده و ضخامت مورد نیاز را برای انواع محصولات تامین میکنند.
کابل عایق شده پس از خروج از کلگی وارد کانال آب خنک شده تا در طول وان به دمای محیط رسیده و در نهایت توسط جریان هوا کاملا خشک شده و در مرحله بعدی کابل از مجاورت دستگاه جت پرینتر عبور میکند تا مشخصات فنی و علامت هایی مانند استاندارد بر روی کابل درج شود. چاپ بر روی کابل حاوی اطلاعاتی مانند نام شرکت , سایز کابل , استاندارد کابل , سال ساخت و ... میباشد و کابل پس از مرحله چاپ به مرحله بعد یعنی دستگاه تیک آپ میرود و روی قرقره جمع میشود
مرحله 5 : روکش زنی
عملیات روکش زنی توسط دستگاهی با نام اکسترودر انجام میشود. مواد اولیه و اصلی این مرحله زیره های استرندر شده گرانول , گرانول و روکش و پودر تالک میباشد.
در کابل های قدرت لازم است که رشته های تابیده شده در دستگاه اکسترودر توسط لایه ای از مواد پلی اتیلن یا PVC روکش شوند و این لایه نقش محافظت مکانیکی برای کابل را دارد.
مرحله 6 : بسته بندی
در فرآیند تولید تقریبا آخرین مرحله ای که وجود دارد فرآیند بسته بندی است. در این مرحله محصول نهایی در متراژ و شکل و نوعی که مشتری درخواست کرده است بسته بندی میشود. سیم و کابل های تولید شده معمولا به دو صورت قرقره و کلاف قابل تحویل به مشتری هستند. در بسته بندی کلافی نیز بر حسب خواست مشتری نوع نایلکس مشخص میشود ولی در نوع اتوماتیک کلاف های سیم و کابل به صورت اتوماتیک توسط دستگاه بسته بندی و وکیوم میشود
محصولات تولید شده با توجه به نیاز مشتری با متراژ مورد نظر بر روی قرقره های چوبی , دوبارپیچ یا لفافه پیچی میشود و پس از پلاک زنی و چاپ مشخصات بر روی آن به قسمت تست نهایی انتقال داده میشود. البته جنس قرقره ها بنا به کارخانه های مختلف میتواند متقاوت باشد و از جنس چوب و یا از جنس آن فلز باشند.
در این مقاله سعی کردیم تا شما را با مراحل صفر تا صد تولید سیم و کابل در کارخانه های تولیدی آشنا کنیم و امیدواریم مطلب مفیدی را برای شما ارائه کرده باشیم. جهت اطلاعات بیشتر و خرید محصولات میتوانید از طریق پل های ارتباطی با کارشناسان ما در ارتباط باشید.